Shapeshifters
3D Printing the Future
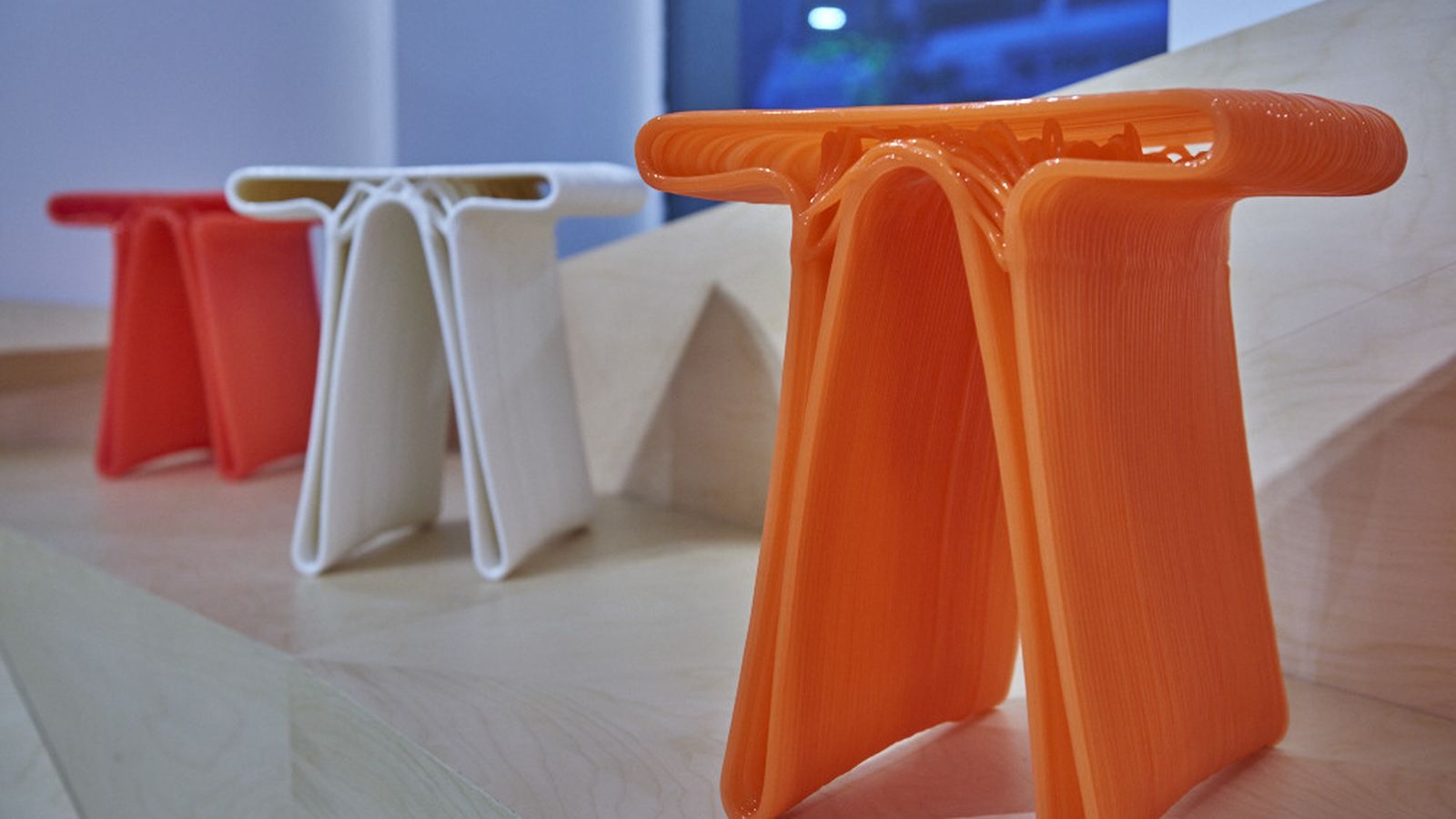
Australian Design Centre
5 May - 20 July 2016
Touring nationally
Western Plains Cultural Centre, Dubbo
23 Jan - 17 Apr 2016
Sturt Gallery, Mittagong
31 Jul - 11 Sep 2016
Devonport Regional Gallery, Devonport
30 Sep - 13 Nov 2016
Design Tasmania, Launceston
25 Nov 2016 - 21 Feb 2017
Wagga Wagga Art Gallery, Wagga Wagga
18 Mar - 7 May 2017
Gladstone Regional Art Gallery & Museum
19 May - 15 Jul 2017
Glasshouse, Port Macquarie
9 Sep - 19 Nov 2017
Redland Art Gallery, Brisbane
21 Jan - 25 Mar 2018
The Workshops Rail Museum, Ipswich
19 May - 2 Sep 2018
What if 3D printing gave you the ability to design your own life? With clothes being printed from desktop computers and organs being manufactured in labs, this rapidly evolving technology continues to revolutionise design as we know it.
In collaboration with Western Plains Cultural Centre, the Australian Design Centre launches Shapeshifters: 3D Printing the Future as a playful exploration of 3D printing. It’s all about imagination, innovation and new methods of making, drawing on the high-tech and rapidly evolving world of 3D printing and fluid extrusion methodology.
3D printing is also built on sharing. Open source software and shared maker spaces mean anyone can try their hand at creating. During the industrial revolution, the machine was used to standardise everything. Now mass production is replaced by mass customization.
The designers and makers in the exhibition all begin with a real world idea. That idea is translated into a digital something – a piece of code, a CAD model or perhaps a verse of music – before being transformed into the final physical form. By experimenting with digital fabrication technologies, the designers build on their traditional modes of making to create something entirely new.
Featuring Louis Pratt, Michael Eden, Lousje Skala, Ryan Pennings, Dr David Ackland, Lukasz Karluk, and XYZ Workshop (Kae Woei Lim & Elena Low).
Explore the Shapeshifters education kit
Learn 3D Printing and CAD Workshops
Discover 3D printing stories on ADC's Flipboard
Download Room Sheet
Explore Shapeshifters on Vimeo
Read Shapeshifters 3D printing case studies
Image: Ryan Pennings, Percy Stools, 2015, Photo credit: Simon Cardwell
'This country has a deep and rich history of making, and making is essential to our existence. Perhaps there's never been a more exciting time to be a maker, but there's certainly never been a more precarious time to be a ‘creative'.
Investment in the arts and culture, and a respect for the deep traditions and the evolution of our culture is what we should be all be supporting. This is what the ADC has fostered for so many years.
This exhibition is proof that we should continue to celebrate the complex engagement with material culture that gives meaning, purpose and utility to all of our lives.'
Professor Ross Harley, Dean of UNSW Art & Design. Excerpt from the Shapeshifters:3D Printing the Future opening night speech 5 May 2016 at Australian Design Centre.
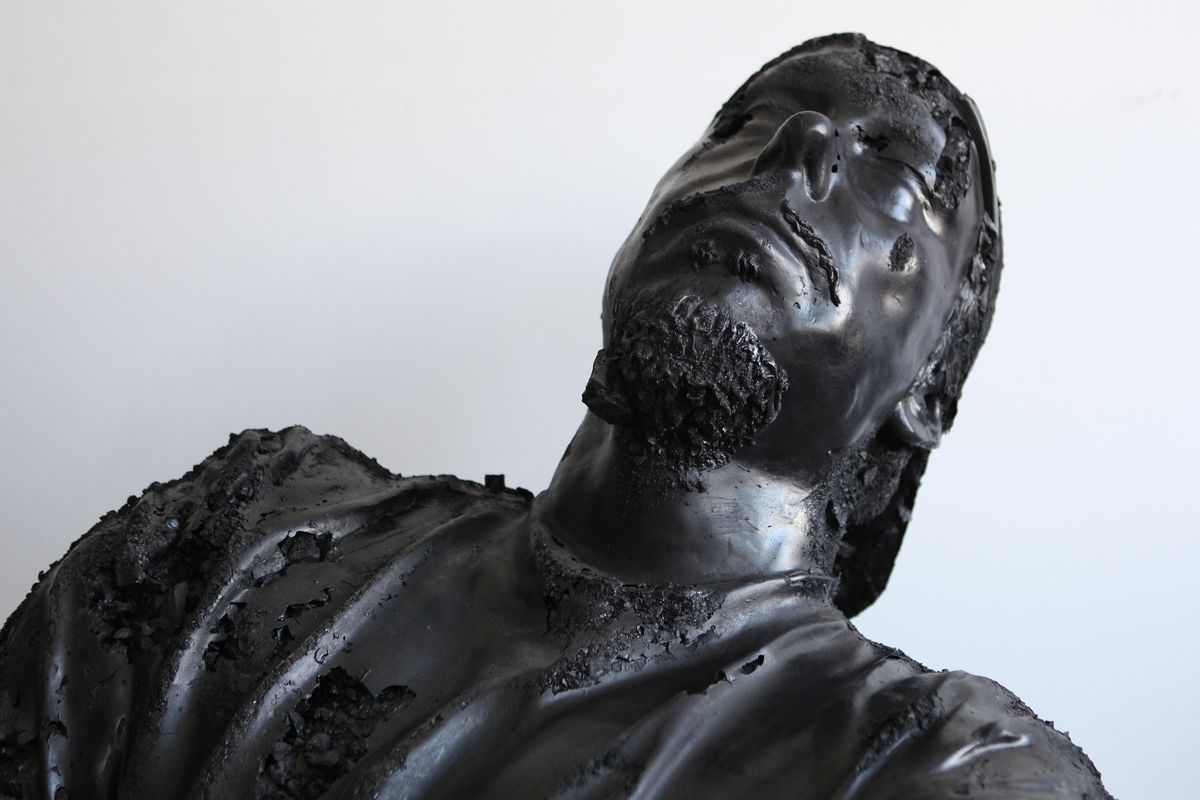
Louis Pratt
Louis Pratt’s King Coal differs from the other objects in the room - the surface you see is not actually 3D-printed. Its what’s underneath that counts. He created the mould for the work with a 3D scanner and printer. In order to produce such a large sculpture from the relatively small printer in his studio, he broke up the data from the scan into parts, printing each in smaller sections. 2000 printing hours later, the mould was complete. Louis’ work is well known nationally and internationally, including Sydney Contemporary and Mt Buller Sculpture Prize.
Image: King Coal, 2015, Louis Pratt
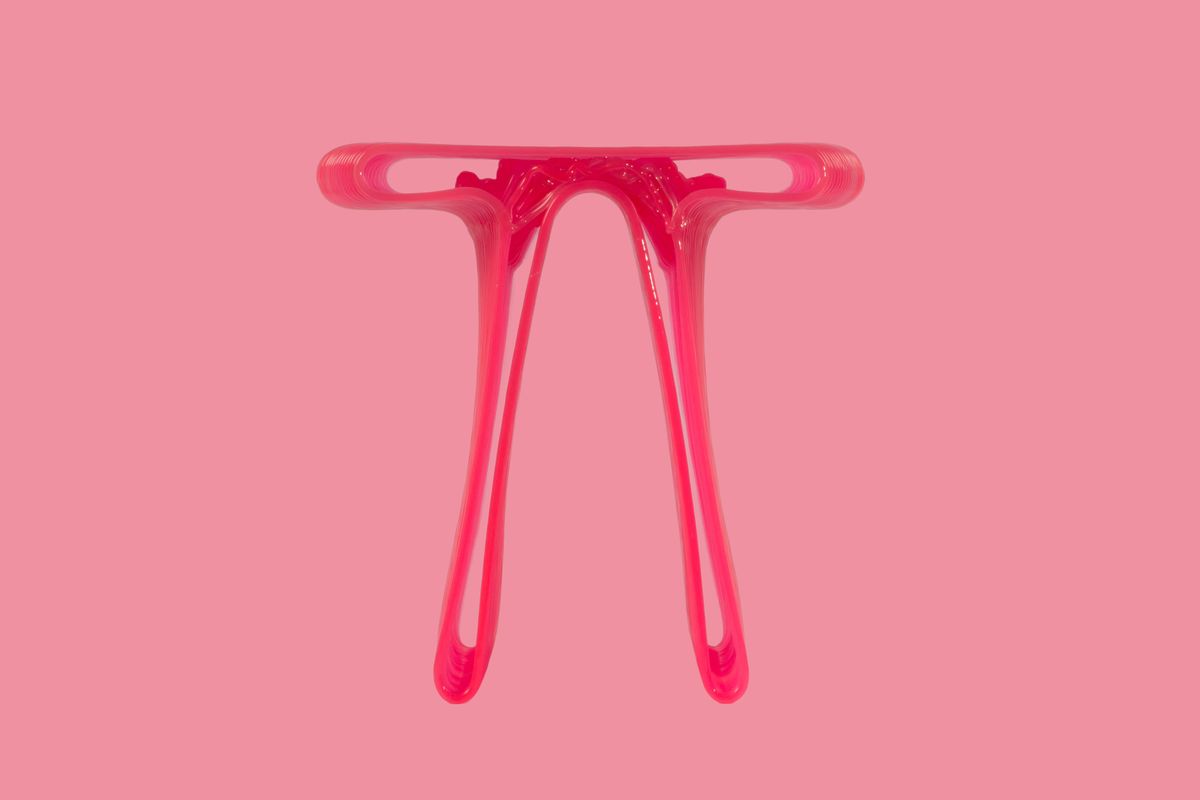
Ryan Pennings
Ryan’s work explores the exciting design opportunities where algorithmic design meets robotic fabrication. As an emerging designer, he tests how algorithmic design can be applied to conventional products. He demonstrates that custom printing furniture for our own homes could be a reality in the near (very near) future. Each stool has its very own algorithm and is printed with a robotic arm. Percy Stools were first developed in 2015 as part of research for Ryan’s Bachelor of Industrial Design (Honours) at RMIT University in Melbourne.
Image: Percy Stool, 2015, Ryan Pennings
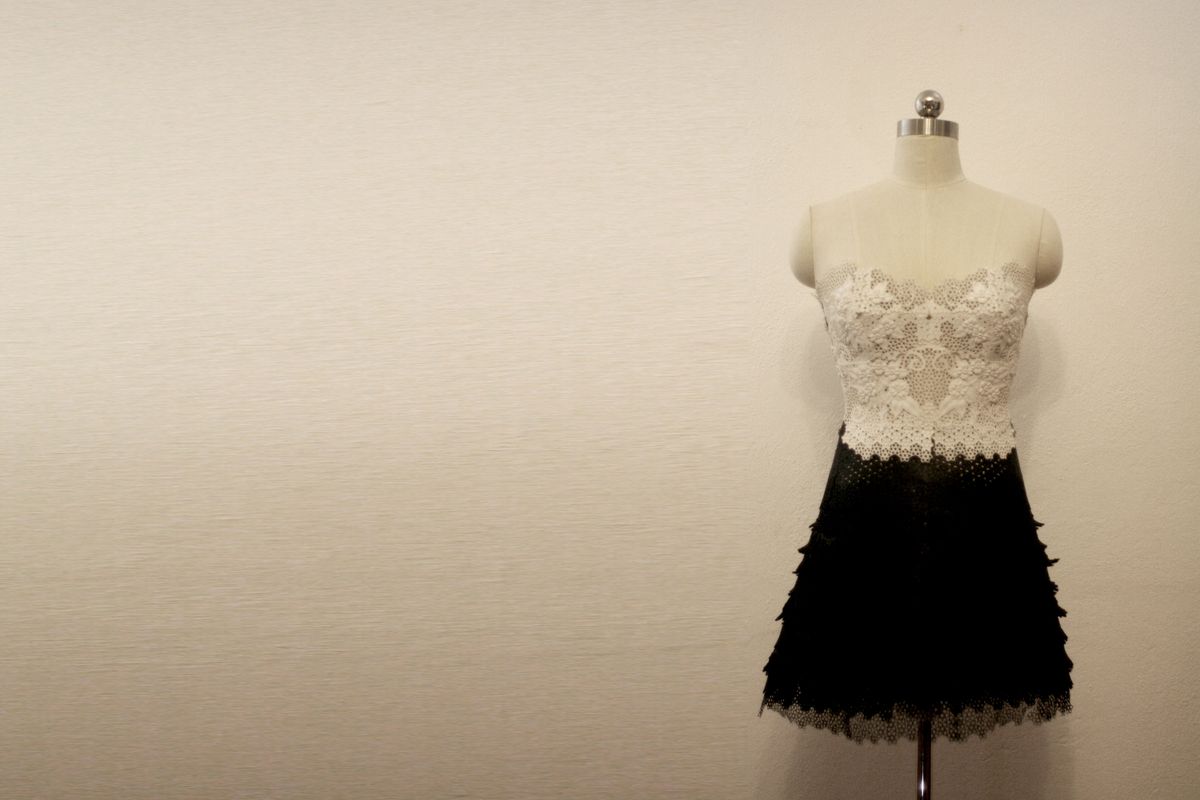
XYZ Workshop
At 2.1meters long, XYZ Workshop has created one of the world’s longest 3D-printed dresses using (only) a desktop printer. Blending traditional dressmaking techniques with digital technology, inBloom makes polylactic acid (PLA) function like textile. The open-source files of the dress are free to download, encouraging people to ‘hack’ the dress and make it their own. In 2014, inBloom made it into the White House for Reach Higher's Fashion Education Workshop organised by Michelle Obama.
Image: inBloom, 2014, Kae Woe Lim & Elena Low

Lukasz Karluk
Holodecks focus on transforming sound through different mediums. Lukasz uses software to transform sound into 3D-printed sculptures. Using a computer generated code, each sculpture is a representation of audio from a selected song. An augmented reality app tracks the rotating sculpture and overlays a virtual 3D model, giving the effect of an audio reactive sculpture. Got it? His interaction design company, Code on Canvas, have produced installations and generative computer art for Sydney Festival, Vivid Light and Australian Fashion Week. They think outside the box.
Image: HoloDecks, 2014, Lukasz Karluk

Lousje Skala
Lousje Skala is a silversmith. Trained traditionally, she has expanded her skills and resources to include non-traditional tools, such as computeraided design software, 3D printing and CNC milling. She is fascinated with language, social disconnection, and the negative social impact of digital media. It is her intention that when people wear her bold jewellery, the pieces encourage social connections. In 2013, Lousje featured in Melbourne Now at the National Gallery of Victoria’s major exhibition, and she has also exhibited across the globe from Europe and Japan.
Image: Calgary Necklace, 2015, Lousje Skala
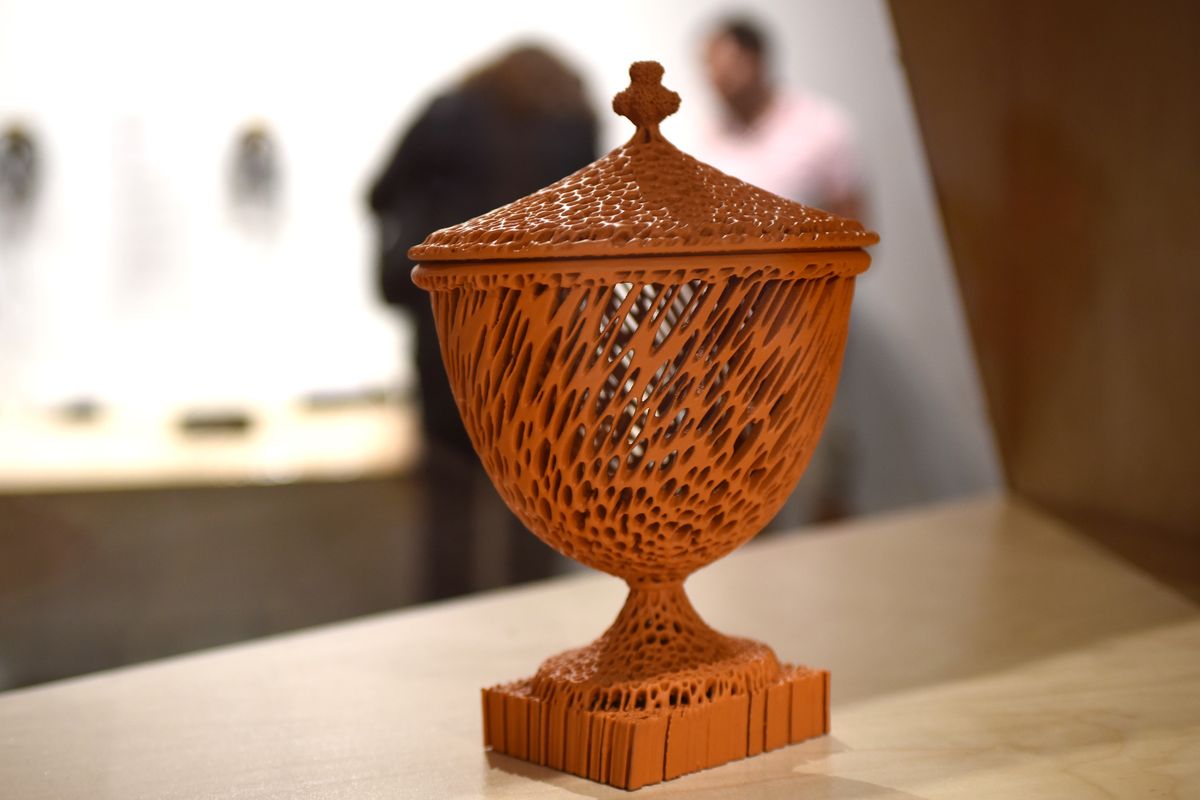
Michael Eden
Since 2008, Michael has been investigating the relationship between the handmade and digital tools. After spending 25 years as a ceramicist, 3D printing offered this British maker a new way of working. It’s clear that A Twisted Oval Wedgwoodn’t Tureen simply couldn’t be made under the limitations of wheel and clay. Michael has paved the way for a new generation of artists to explore the creative freedom that 3D printing provides. His work has been exhibited at the Museum of Arts and Design & Cooper-Hewitt in New York, Victoria and Albert Museum in London and the Museum of Fine Arts in Boston.
Image: A Twisted Oval Wedgwoodn't Tureen, 2012. Courtesy of Adrian Sassoon, London.
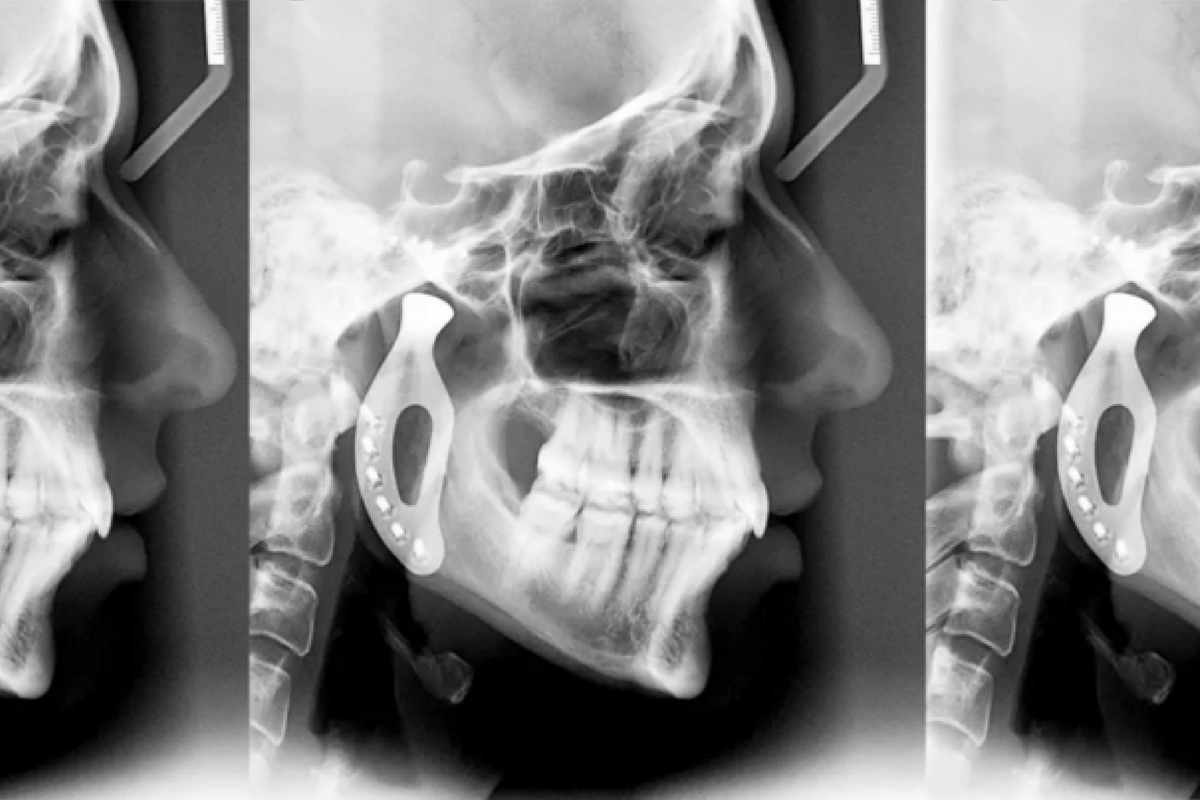
Dr. David C. Ackland
David is a bioengineer and a senior lecturer in the Department of Mechanical Engineering at the University of Melbourne. His team at UoM collaborated with surgeon George Dimitroulis to design a prosthetic joint replacement using musculoskeletal modeling techniques. The joint was 3D-printed in titanium before being implanted into the patient. The prosthesis is set to improve the quality of life of countless others. It will revolutionise joint replacement surgery, allowing the creation of fully customised implants tailored to the anatomy of each patient.
Image: 3D-printed Prosthetic Joint Replacement for the Human Jaw, 2015. Courtesy of the University of Melbourne